

However this benefit can only be availed if cost of holding inventory is taken care off. Thus it is important to invest in the inventories and save whenever the price of the materials goes up.
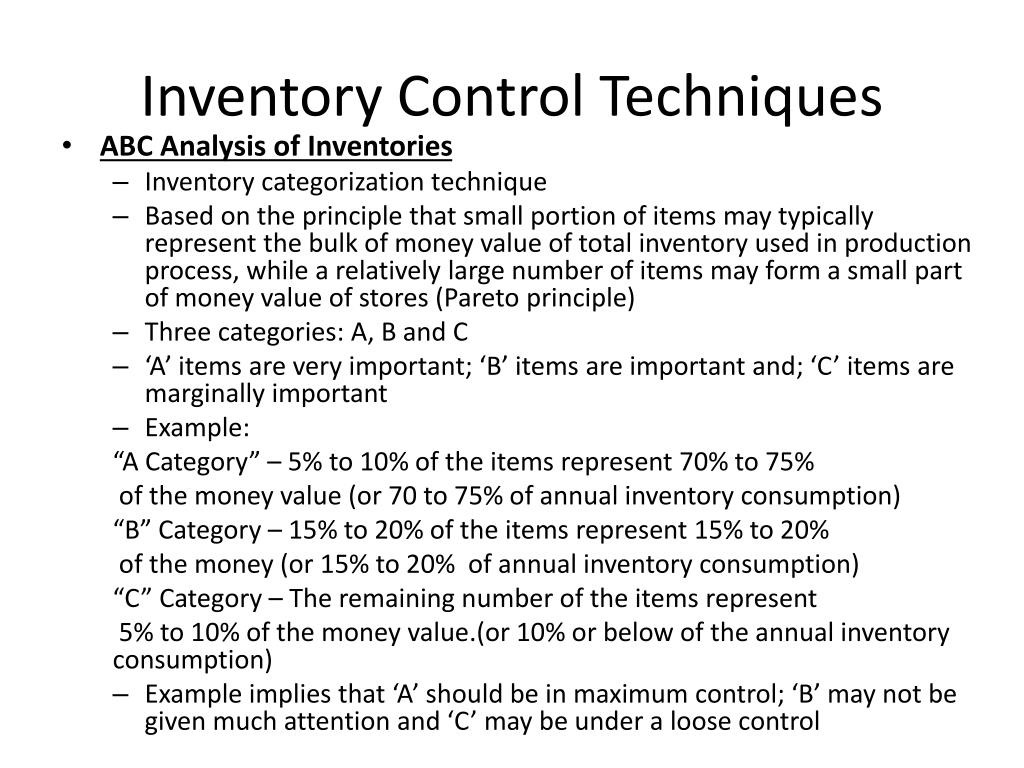
To keep inactive, waste, surplus, scrap and obsolete items at the minimum level.to its users as per their requirements at right time and at right price.
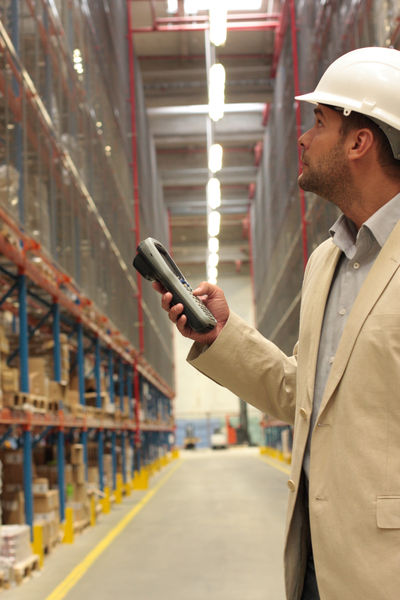
To supply the product, raw material, sub-assemblies, semi-finished goods etc.To maintain the overall investment at the lowest level, consistent with operating requirements.Inventory control is the technique of maintaining the size of the inventory at some desired level keeping in view the best economic interests of an organization.It is possible to exercise control over three types of inventories recognized by accountant as raw material, work in progress and finished good. Inventory control may be defined as planning, ordering and scheduling of materials used in the manufacturing process.Inventory control is concerned with various items stocked at predetermined level or within some safe limits.Inventory control is a system of ordering based on the maintenance of the stock in a store using a re-order rule based on the stock level.Systematic management and control of inventory for all the items is a challenging job. A inventory is an essential part of any organization, it consists of many items running into thousands. The present concept of inventories has necessitated the use of scientific techniques in the management of inventories known as inventory control.
